Leyland P76 Owners 2003 |
Technical problem |
|
Now it's time for another Philthy Tech Tip!
- This Tech Tip deals with the Kettering Curse! Yes, folks, I'm not the only non-tech P-nut in our wonderful Club who still has points flickering away in his distributor. Out there in P-76 land, there are literally dozens of P-nutz who are still using this system, which as we all know does not require the use of a diagnostic computer at tune-up time! However, there are a number of things, which we need to do to gain maximum service life and efficiency from our ignition systems when we're still using points to spit the spark.
- For starters, fabricate a solid metal bracket and mount the coil nearer to the distributor. A shorter primary lead from the coil to the distributor cap means less resistance to the "spark", and that means a small gain in efficiency. Next, fit one of the newer ballast resistors to the system. The older styles of resistor are much more likely to fail at some inconvenient time, usually due to the resistor element breaking. This will give you an open circuit, and a total lack of spark. If this happens while you're driving along, the effect will be similar to someone turning the ignition key to the "off" position, ie, a dead engine!
- Note that if your resistor does fail in this manner, you will still have spark while the starter motor is turning, and your engine will start to run, provided that your resistor by-pass wires are intact and connected properly, but when your ignition key returns to the lion" position, the engine will stop running due to the break in the ignition circuit caused by the broken resistor element. To cheek the condition of the ballast resistor in these conditions, simply pull the while power supply wire off the resistor terminal, and push it directly onto the coil "+" terminal. If the engine now turns, starts, and continues to run, then your resistor is faulty. Caution- if you leave a 12 volts resistance-type coil connected to a 12 volts supply for more than a few minutes, you risk burning out the coil, so in an emergency, you can use a spare tail-light globe and socket as a temporary resistor. Plug one of the spade terminals from the socket to the "+" supply wire, and fit a female crimp terminal to the other wire so you can fit it to the coil "+" terminal. At least this repair should get you home without cooking the coil.
- Now we come to the points. These are a hard-working little item, and although they are often cursed as being a really nasty idea, the truth is that in 90% of situations where ignition problems are encountered, the fault really lies either in the manner in which the points have been installed, or adjusted, or else in some other component. As an electrical switch, a set of points has a pretty hard life, and if you do the sums, calculating how many times in say, a three-month period of everyday use, a set of points opens and shuts while doing service in a V-8 distributor, you will soon see that, all things considered, they do a rather good job! Now, let's look at a few tips on installing and setting points which should help you get better service from them.
- 1). The contact faces of new points are usually coated with a small amount of preservative grease which will do a good job of blocking the flow of current if it's not removed, so the first job is to wipe the points faces with a small piece of rag soaked in solvent, to remove the grease.
- 2). Sometimes, it also helps to lightly abrade the point's faces with a fine grade abrasive paper, to ensure good electrical conductivity.
- 3). To operate properly, the pivoting arm of the points must move freely on the pivot post. Some of the sets of points recently marketed have needed attention to the tolerances or clearances between the plastic pivoting arm and the metal pivot post, to cure a small amount of stiffness.
- 4). In addition, the metal spring arm on some points sets may need to be shimmed up away from the metal base with two or three small fibre washers so that it doesn't twist or distort when the locking nut is wound down onto the threaded spindle / post / whatever the hell you want to call that little metal stud onto which you secure the terminals from the condenser and coil negative (-) wire.
- 5). For the points to operate properly, the terminals on the wire' from the condenser and the coil negative wire must be electrically insulated from any earth contact with the points metal base plate, or the body of the distributor, etc. To achieve this, a small stepped plastic insulator is supplied with each set of points. The terminals on the wires from the condenser and coil negative lead are fitted to the smaller diameter section of the plastic insulator, and the insulator is then carefully fitted onto the threaded stud / thingy/ post, and then the little nut is tightened to hold everything firmly in place. Please note that these little nuts have been carefully designed so that when you accidentally drop them, it is almost totally impossible to find them, no matter what kind of surface you drop them on!
- 6). The screw which secures the points base plate to the pivoted base plate in the distributor body has the same thread as those fine screws which hold most of a P's dashboard together, so you don't need to panic if you lose the original one! All you need to do to make a workable substitute is grind down the threaded portion of a spare dashboard screw to approx 3/16" length.
- 7). To set the points gap, carefully rotate the engine in its normal direction of rotation until the "10 degrees before top dead centre" timing mark on the crankshaft pulley aligns with the point of the timing marker on the body of the water pump. Next, loosen the distributor clamp bolt, so the distributor body can be turned.
- 8). Turn the distributor body slowly clockwise and watch as the plastic heel of the pivoting arm of the points "rises" as it meets the lobe of the distributor spindle. When the heel is on the peak of the spindle lobe, temporarily re-tighten the distributor clamp bolt.
- 9)I prefer to set the points in Targy to 12 to 13 thou, and I find that getting the correct adjustment is easier if I use one flat-blade screwdriver in the adjusting slots in the base plates to adjust the points gap and hold them in place, while using another screwdriver to tighten the securing screw.
- 10). When the adjustment is correct, loosen off the clamp bolt, and turn the distributor body slowly counter clock-wise until the points appear to close fully. Turn the Ignition "on". Again, slowly rotate the distributor body counter-clockwise until you see or bear the small spark as the points just crack open. A definite spark is a sign of good conductivity. A weak or faint spark can indicate problems in the system, such as dirty connections, or a faulty condenser.
- 11). Re-tighten the distributor clamp bolt. Your timing should now be pretty close to 10 degrees BTDC, set statically.
- 12). Remember to check that the little nut that holds the condenser and coil lead terminals is tight, and also check that the points screw is tight.
- 13). Check the condition of the low-voltage connections on the coil. These have a nasty habit of looking alright, but there is often corrosion lurking underneath the connectors, which can easily cause misfiring and rough idling, so take them off the terminals for a good cleaning.
- 14). Remove each spark plug lead end from the distributor cap, and check the condition of the contacts inside the individual terminals of the cap. Again, corrosion, dirt or Moisture in this contact can cause mis-firing, or rough idling. A light spray with a good brand of W.D. spray will help to maintain good electrical conductivity
- 15). One last item to check is the operation of the advance weights and mechanisms in the base of the distributor. While the distributor cap is removed, fit the rotor button to the distributor spindle, or shaft, and turn it a few degrees clockwise, which is imitating what happens when the mechanical advance mechanism is "advancing" the spark. When you release the pressure on the rotor button, it should return fully to its original position. If it appears to stick
- in a slightly advanced position, it may be necessary to strip the base plate out of the distributor body, and carefully re-tension the advance weights springs. Note that the rotor button should be able to move only a few degrees before spring pressure restricts its movement. I have found that with the crappy low-octane fuels, which we've been sold lately, a reduction in the amount of advance in the ignition timing has helped to reduce the amount the engine "pings" when under load. If the distributor spindle does appear to be sticking in the advanced position, a thorough cleaning of the mechanism inside the distributor body should cure the problem.
- 16). Targy is still running quite happily with an original-style of Lucas coil, which might mean that the coil is as old as the car! The most common reason for replacing a coil is when the insulation at the end of the coil falls, and the high-voltage spark develops the habit of "tracking" from the insulated nose of the coil, across to the low voltage terminals, causing a major mis-fire. I have found that a few carefully placed blobs of Silastic around the low-voltage terminals will help to prevent voltage loss.
- 17). Finally, a good way to cheek on the general condition of the sparky stuff on your P Is to pop the bonnet one dark night, and let the engine idle for a while, while you have a good look around the engine bay. 1 have used this method on a few occasions to detect a faulty spark plug lead, or a cracked distributor cap, or a coil with a spark "leak" at the high-voltage end.
- One lesson which has been reinforced by my recent experiences while rebuilding Kerry's Blue P and Danny's Bitter Apricot Super, is that you just cannot leave anything to chance. That one thing you don't actually check, clean or adjust, will be the one thing which plays up a bit later on, causing you unnecessary delays and giving you a big dose of the tomtits. Remember, we're dealing here with cars and components which are about to celebrate their 30 th birthday, so now, more than ever, aim for maximum reliability, leave nothing to chance and be thorough when you're servicing your P.
|
|
|
|
Last updated Feb, 2006 |
This web site may contain Copyright material
If you find any problems with the site, please email the
Web Editor 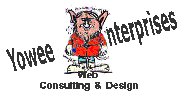 |
|